- Plan My Baby: A Modern Guide to Family Planning
- Exploring the Concept of Slot: A Space of Opportunity and Chance
- The Fascination of Slot Machines: From Classic Reels to Digital Spins
- Difference Between Workers’ Comp Doctors and Regular Physicians in Rego Park
- The Fascinating World of Slot Machines: A Unique Blend of Chance and Entertainment
The Art and Science of Stainless Steel Casting
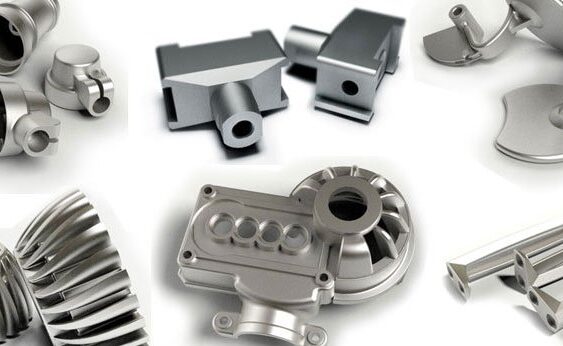
Introduction: Stainless steel casting is a versatile and highly efficient manufacturing process that has revolutionized the way we create intricate and durable metal parts. This method offers numerous advantages, including precision, strength, and corrosion resistance, making it indispensable in a wide range of industries. In this article, we will explore the art and science behind stainless steel casting, from its history to its modern applications.
The History of Stainless Steel Casting
Stainless steel itself has a fascinating history, and its discovery and development are intrinsically linked to the evolution of casting techniques. In the early 20th century, the development of stainless steel by metallurgist Harry Brearley marked a breakthrough in materials science. It was corrosion-resistant, heat-resistant, and incredibly strong, making it an ideal candidate for various applications. However, it wasn’t until casting technology advanced that the full potential of stainless steel could be harnessed.
Casting, in general, dates back thousands of years to ancient civilizations such as the Egyptians, who used sand casting to create intricate jewelry and small artifacts. The principles of casting remained relatively consistent throughout history until the industrial revolution, which saw the emergence of more advanced casting techniques.
The Art of Stainless Steel Casting
Stainless steel casting is an art as much as it is a science. Skilled artisans and engineers work together to design intricate molds and patterns that will ultimately determine the shape and structure of the final product. Let’s delve into the key steps of the stainless steel casting process:
- Pattern Creation: The process begins with the creation of a detailed pattern, which serves as a template for the final product. These patterns can be made from various materials, including wood, wax, or 3D-printed plastic.
- Mold Preparation: The pattern is use to create a mold, typically made from a mixture of sand and bonding agents. This mold is formed around the pattern and harden to create a negative impression of the desire part.
- Melting and Pouring: Stainless steel, in its raw form, is heat to a molten state, often using electric induction or other high-temperature methods. Once the steel is at the right temperature, it is poure into the prepared mold.
- Cooling and Solidification: The molten stainless steel cools and solidifies within the mold, taking on the desired shape and characteristics.
- Removal and Finishing: After the metal has fully solidify, the mold is broke open, revealing the newly cast stainless steel part. These parts often require additional finishing processes, such as grinding, polishing, and machining, to achieve the desired specifications and surface quality.
The Science of Stainless Steel Casting
While there’s a significant artistic component to stainless steel, it is firmly root in scientific principles. The choice of stainless steel alloy, the precise control of temperature and cooling rates, and the understanding of metallurgy are all crucial to the process.
Stainless steel alloys can vary significantly in composition, each offering distinct properties. Common alloys include 304 (an all-purpose grade). 316 (known for its excellent corrosion resistance), and 17-4 PH (chosen for its high strength and durability). The selection of the appropriate alloy is crucial to achieving the desired performance characteristics of the final product.
The control of temperature during the melting and pouring phases is critical to ensure proper flow and solidification of the stainless steel. It helps prevent defects like porosity and inclusions.
Cooling rates are also precisely controll to manage the transformation of the molten stainless steel from liquid to solid. This control affects the grain structure and overall material properties.
Metallurgy plays a vital role in stainless casting. Understanding the behavior of stainless steel alloys. The casting process is essential for ensuring the quality and performance of the final product.
Applications of Stainless Steel Casting
Stainless steel casting has a wide range of applications across various industries, including aerospace, automotive, healthcare, and more. Some common applications include:
- Aerospace: Stainless steel components for aircraft engines, landing gear, and structural parts benefit. The material’s corrosion resistance and high-temperature performance.
- Automotive: Steel casting is use for exhaust manifolds, turbochargers, and other components that require high-temperature resistance and durability.
- Medical: Stainless steel is an ideal choice for medical instruments and equipment due. Its biocompatibility, corrosion resistance, and ease of sterilization.
- Food and Beverage: Stainless steel components for processing and packaging equipment are vital for maintaining hygiene and preventing corrosion from acidic or caustic substances.
- Energy: In the energy sector, stainless steel is use for components in power generation. Including turbines, valves, and pumps, due to its resistance to high-temperature and corrosive environments.
Conclusion
Stainless steel casting is a remarkable combination of art and science that has shaped the modern industrial landscape. It allows for the creation of complex and durable parts used in a wide array of industries. As technology continues to advance, stainless casting methods and materials will only become more sophisticated. Opening new possibilities for innovative applications and ensuring that this age-old technique remains a pillar of modern manufacturing.