- Slot Machines: Spinning Through History, Innovation, and Entertainment
- The Ever-Spinning World of Slots: A Unique Look into Their Evolution and Appeal
- The Fascinating World of Slot Machines: Luck, Technology, and Entertainment
- EmakQQ: Platform Domino QQ Online Terpercaya di Indonesia
- JepangQQ: Platform Permainan Kartu Online dengan Nuansa Modern
The Process of Polythene Products Manufacturing in the UK
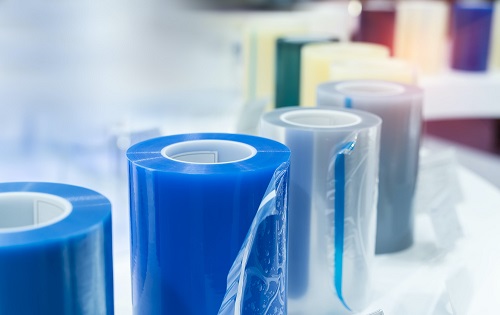
Polythene Products – Natural in colour with good clarity. Flexible and pliable with good tensile strength HDPE – Natural in colour with cloudy appearance. Stiffer more rigid film with high strength properties LLDPE – Is a polymer which when added increases performance particularly in it strength characteristics MLDPE – This is linear polythene, with good strength characteristics, again natural in col-our Film Substrates Virgin Reprocessed Mixed Density Co-extruded
- Virgin: Extruded from its natural Material for more critical and consistent Applications
- Reprocessed: Extruded from recycled polythene for non critical applications such as waste bags
- Mixed Density: Mixing polymers together to form different characteristics.
- Co-extruded: Multi layered polythene containing different polymer grades. Polythene Additives
Masterbatches
Polythene is natural in colour and masterbatches are add to give its colour. Different % of masterbatches is add to give the polythene its opacity of colour. For a hint of colour about 1-2 % is add to give it a tint. For a deep colour where the polythene needs to opaque between 6 and 12% addition Only certain colours have good opacity properties e.g. White cannot opaque so co-ex (multi layered) needs to be make with a coloured inner layer.
Bio-Degradable
This is an additive that we add to the film to make it degrade, there are a number of different additives on the market which we use.
The Polythene Manufacturing Process
The Blown Film Process
The blown film process is the method by which the vast majority of all polythene products are manufactured. Polythene granules are fed into an extruder. As the granules are transported down the extruder screw, they are continuously heated and eventually become molten.
The melt passes through a narrow slit forming a tube which is extrude vertically until it can clamped at the top nip rollers, which continuously pull the tube from the die. Once clampe the tube is inflate to create the desire width, the speed of the nip rolls determines the film thickness. The film is air cool to set the film dimensions.
The tube is then collapse prior to the nips to form a lay flat tube to a set width and thickness. The flat film is pass through path rollers to a floor mount winder. Further processing can take place during this section for example: Slitting, Trimming, Perforation or treatment for print.
The cast film process
In the cast film process the material is forced through a slit die to form a sheet. The sheet is (as with blown film) drawn off via nip rolls again the wall thickness is determined by the speed at which the material is drawn off.
Cast film is cool as it exits the die via large water cool chill rolls which also leave a micro embosse pattern on the film. Winding styles and terminology Lay Flat Tube (LFT). The most basic blown film product – formed by collapsing and flattening the bubble / tube. All other blown film products are derive from the lay flat. Centre Fold Sheet (CFS) – This is a lay flat tube with one edge fold remove by either a trim or an edge slit. Single Wound Sheet (SWS) – Again both edges of the edge fold are remove. In this instance the two sheets of film are separated and are wound up simultaneously. As with double wound sheet (DWS), the roll can now slit down into multiple rolls by inserting slitting Blades. Because cast film is extrude through a ‘slit die’ the final product is exclusively Single Wound Sheet.